In modern building insulation systems, two of the most widely used rigid foam materials are Polystyrene and Polyurethane Insulation Boards. Though they may look similar in appearance, their chemical structure, thermal behavior, and performance in real-world applications vary significantly. Choosing the right insulation material is not just about cost—it’s about efficiency, safety, durability, and environmental compatibility.
Material Composition: The Foundation of Performance
Polystyrene insulation boards—including EPS (Expanded Polystyrene) and XPS (Extruded Polystyrene)—are made from polystyrene resin, a thermoplastic polymer that expands when exposed to heat.
- EPS is created by molding small beads of polystyrene, which are expanded with steam.
- XPS is made by extruding molten polystyrene into continuous sheets, making it denser and more uniform.
In contrast, Polyurethane insulation boards are derived from the chemical reaction between polyol and isocyanate, forming a rigid thermoset foam. The more advanced variant, PIR (Polyisocyanurate), has a modified molecular structure with enhanced fire resistance and thermal stability.
This fundamental difference in polymer chemistry leads to dramatically different behavior across several performance metrics.
Thermal Insulation: Why Polyurethane Leads
Thermal conductivity is a key metric in insulation performance.
Polystyrene boards (EPS: ~0.035–0.038 W/m·K; XPS: ~0.029–0.033 W/m·K) offer moderate insulation efficiency per unit thickness.
Poliuretano (PU) and especially PIR boards deliver superior performance (~0.020–0.024 W/m·K), making them ideal for achieving high R-values in thinner wall profiles.
For energy-conscious buildings or cold storage, polyurethane provides better insulation with less material, helping save space and improve energy ratings.
Water Resistance and Moisture Behavior
While both materials are closed-cell foams to some extent, their resistance to water differs due to density and pore structure.
- XPS performs well in wet conditions due to its high density and consistent pore structure.
- EPS is more permeable and can absorb moisture over time if not properly sealed.
- PU/PIR boards are highly hydrophobic and resist both water absorption and vapor penetration, making them suitable for humid environments and below-grade insulation.
In long-term use, moisture resistance directly impacts thermal performance and material integrity, giving PU-based boards a distinct advantage in damp climates or exposed conditions.
Cutting, Installation, and Workability
From a contractor’s point of view, workability is just as important as insulation value.
Polystyrene boards are lightweight and easy to cut using hot wire or mechanical saws, but they may break or crumble if not handled carefully, especially EPS.
PU/PIR boards are rigid but slightly more brittle; however, they offer cleaner edges when cut and can be precisely fabricated for custom applications such as duct panels or cavity wall linings.
In terms of surface finish, polyurethane boards can be factory-laminated with foil, fiberglass, or other facings for improved handling and performance—something less commonly done with polystyrene.
Fire Performance and Safety
One of the most critical distinctions between the two materials is fire behavior:
Polystyrene, being a thermoplastic, can melt and drip when exposed to flame. It generally needs to be treated with flame retardants to meet building codes.
Polyurethane, especially PIR, has better charring behavior and self-extinguishing properties. Its cross-linked structure does not melt, giving it a clear safety edge in both residential and commercial buildings.
In buildings with strict fire regulations—such as schools, hospitals, and high-rises—PIR foam is often the preferred choice.
Environmental Considerations
In today’s sustainability-focused construction market, insulation materials are also evaluated for environmental impact:
EPS/XPS are recyclable in theory but often not recycled in practice due to contamination and logistics. XPS also has historically relied on blowing agents with high global warming potential (GWP), although many manufacturers now offer low-GWP alternatives.
PU/PIR boards, though more chemically complex, require less material for the same insulation value—meaning less volume, less weight, and lower transportation emissions. Many PIR manufacturers now also use halogen-free blowing agents and offer EPDs (Environmental Product Declarations) for green building compliance.
Summary: Which Is Better?
Feature | Polystyrene (EPS/XPS) | Polyurethane (PU/PIR) |
Thermal Performance | Moderate | Excellent |
Resistência à umidade | Good (XPS) | Excellent |
Fire Behavior | Low | High (esp. PIR) |
Ease of Cutting | Easy but fragile (EPS) | Precise, less messy |
Weight | Light | Light |
Environmental Impact | Low cost, recyclable | Higher performance, more efficient use per m² |
In short, polystyrene is sufficient for basic thermal needs, especially in dry, low-risk environments. But for projects requiring high energy efficiency, fire resistance, or moisture control, polyurethane—especially PIR—is the superior choice.
GFI Duct: Delivering High-Performance Polyurethane Solutions
At GFIDuct, we manufacture and supply premium Polyurethane and PIR Foam Insulation Boards tailored for commercial, industrial, and high-efficiency building applications. With customizable facings such as aluminum foil, kraft paper, or glass fiber, our insulation panels offer unmatched thermal performance, installation convenience, and long-term durability.
Whether you’re insulating a wall, a roof, or an advanced HVAC system, GFI’s pre-insulated boards help you build smarter, greener, and more reliable structures.
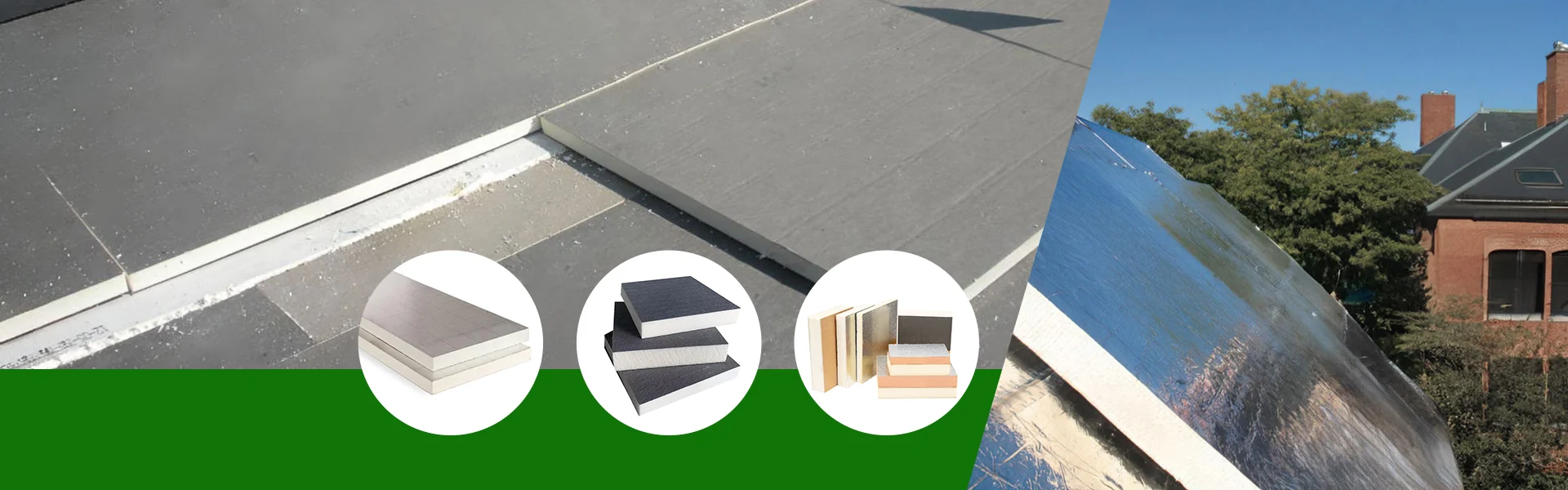